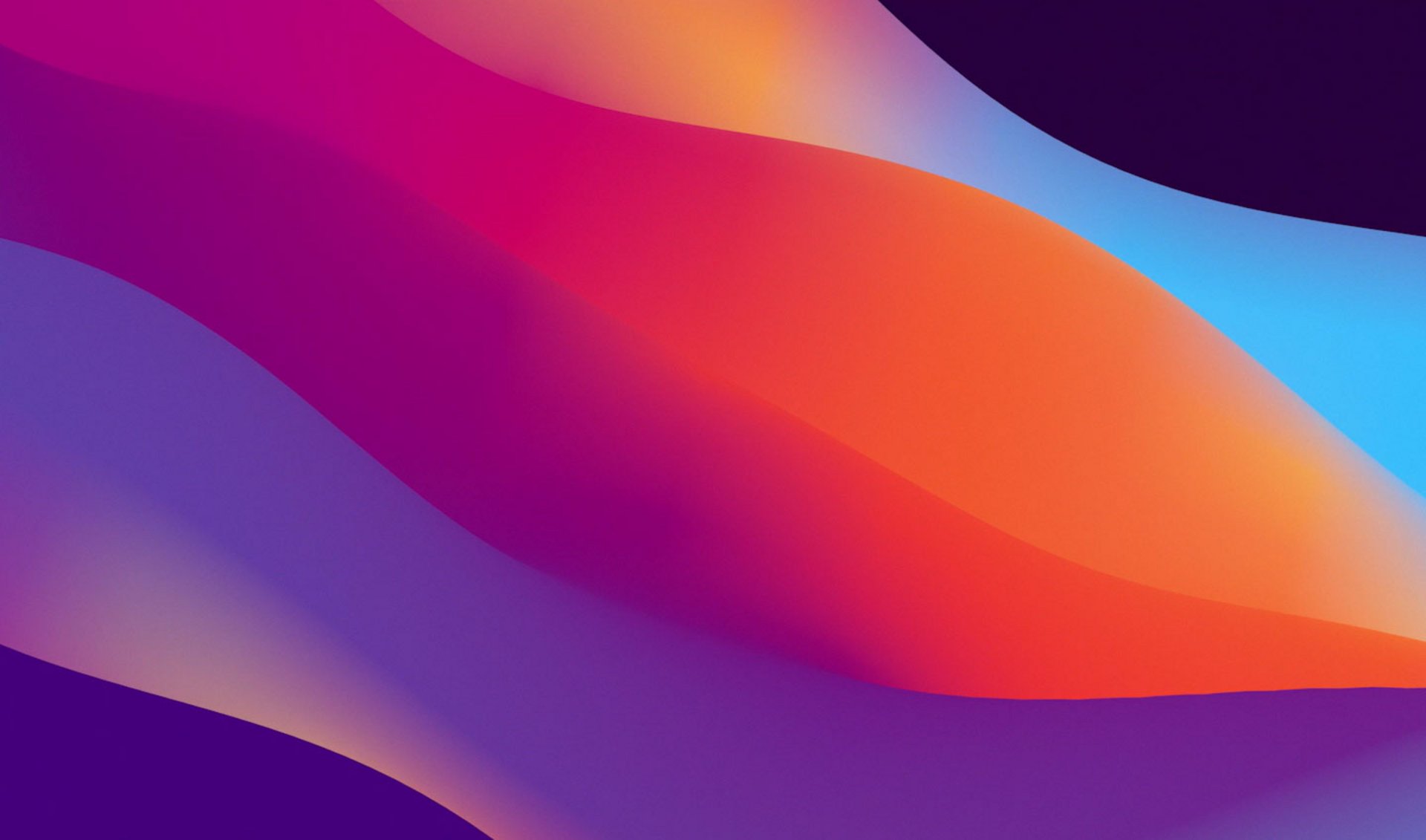
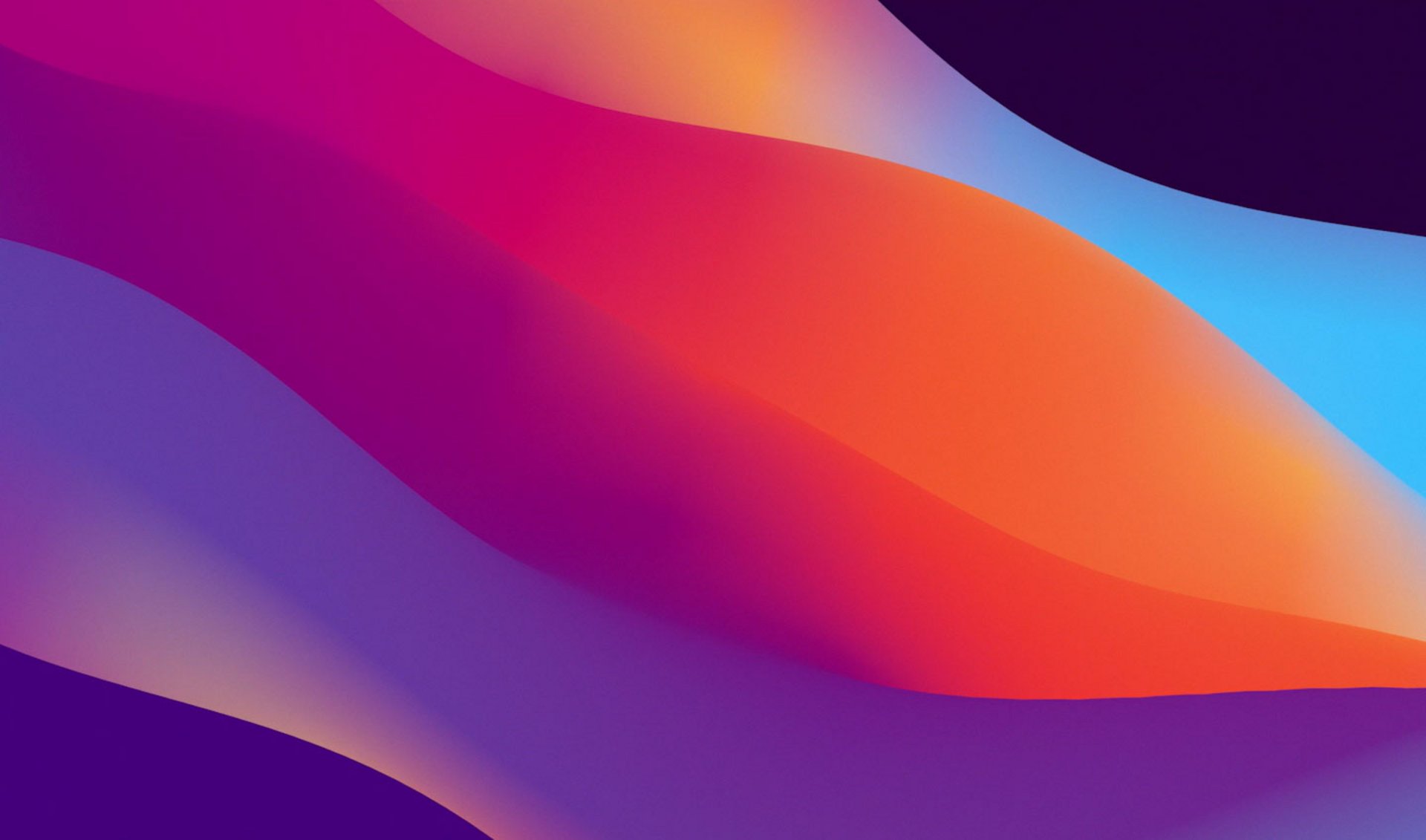
The sCONVEY BS blower station is designed with a filter positioned on top and a blower underneath. This smart arrangement ensures efficient material transport and effective dust separation. With its intelligent, flexible, and automated structure, it is the perfect solution for small, medium, and large industrial plants.
sCONVEY BS
Integrated Design
Pre-assembled unit for efficient use.The sCONVEY BS blower stations consist of a side channel blower, a cyclone dust filter, and a frame, forming a compact unit. All components are pre-assembled at the factory and only require minimal effort to set up on-site – just wiring is needed. This saves time and effort, offering a practical and efficient solution.
sCONVEY BS
Footprint
Space-saving and easy to integrate.The sCONVEY BS blower stations feature a compact design, allowing them to be installed in confined spaces. They promote efficient resource utilisation and so reduce operating costs.
sCONVEY BS
Multiple models
Flexible for every production requirement.The sCONVEY BS blower stations offer a range of blower models from 0.86 to 8.6 kW. Frequency-controlled variants are also available for the 4.6 to 8.6 kW blowers. Thanks to their versatile sizing they are ideal for meeting diverse production requirements.
sCONVEY BS
IE3 blowers
Efficient conveying performance with significant energy savings.The blower station uses IE3 energy-saving blowers. These save energy without compromising efficient conveying performance, operate quietly, are durable, and come with blower protection. A vacuum safety valve on the bypass directs air outward to prevent overload and extend service life.
sCONVEY BS
Cyclone filter
Highly efficient dust removal for flawless materials.The blower station is equipped with a central dust collection filter for efficient dust removal. The filter combines a cyclone separator with a fine dust filter and includes a dust collection bin for easy cleaning. Its cyclone-shaped design ensures reliable fine dust filtration, enabling dust-free material conveying and reducing defect rates in finished products. A differential pressure sensor monitors the filter, and the air implosion cleaning system minimises maintenance effort.